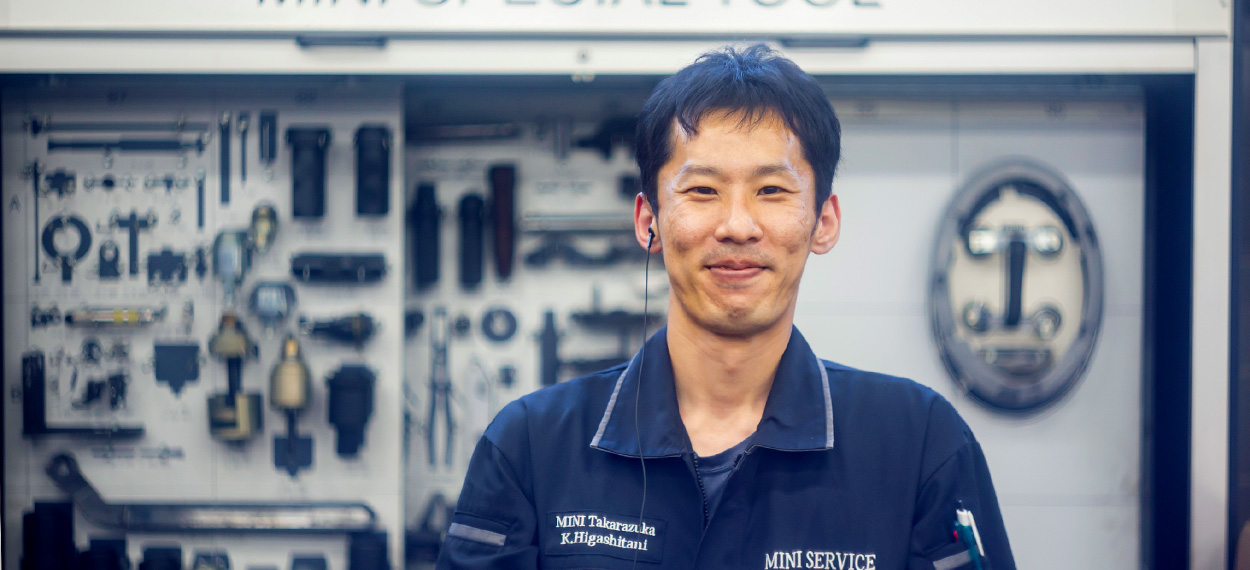
INTERVIEW 01
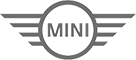
Enjoying work and mastering new skills:
the pride and satisfaction of being a technician.
Joined: 2015
Technician
Began as a mechanic working on Japanese cars
I had always worked on Japanese cars, but as a driver the brand I was really interested in was MINI. One day out of curiosity my wife and I peeked into a MINI dealershp, and we both fell in love at first sight with the second generation John Cooper Works that was on display. It was such a cool car! We were taken by how well it drove, the immediacy of the steering and the sporty setting, so we decided to take the plunge and purchase one. At the time I worked at a used car dealership, but once I started driving a MINI for myself I couldn't help notice how complex and interesting the vehicle was. I wanted to work on them, too.
I found an ad and applied to the dealership where I work now. I had visited it many times as just a customer and was struck by the positive atmosphere inside. Since I had only ever worked on Japanese cars before I was a little uneasy about working on my first imported vehicle, not to mention a premium luxury brand. However, like many technicians who began their careers working on domestic vehicles, once I got started I realized a lot of the knowledge and experience I had built up so far still applied and I started to feel more at ease.
Supported by an extensive training program
The first thing that struck me after joining the company was the skill level of my senior colleagues. It was surprising how much they knew. They weren't just pros when it came to MINI, they could also explain minute details in comparison to competing vehicles from other brands. When it came to handling the vehicles, as well, they would always keep in mind that these cars were the customers' babies. For instance, they would open and close the hoods and doors carefully using both hands to avoid unnecessary shock. I could see right then and there what it meant to be a mechanic for a premium luxury brand.
The training program was much more extensive than I imagined. There are a wide range of training courses available for each level along the way toward Meister, which is the pinnacle of MINI's in-house certification system. There are so countless opportunities to learn new things and improve your skills, as long as you have the motivation. In addition to using the e-learning system, I also attend trainings for several days at the BMW Group Academy locations in Makuhari and Kobe once every three months. The training contents continue to change as vehicle technology evolves. I love that we're always learning about the latest developments.
A comfortable environment where you can focus on repairs
I'm almost in my sixth year of working here, but I'm still amazed by how BMW Group supports technicians in their work. The comfortable work environments they provide are one example. Previously I had only ever worked in semi-outdoor garages where being hot in summer and cold in winter just went with the territory, but at BMW/MINI dealers most workshops are indoors with full heating and cooling. Maintaining a stable environment regardless of season or weather is much less physically demanding and lets us concentrate on our real work.
The majority of day-to-day tasks revolve around inspections, with standard services such as oil changes or preparing new vehicles for delivery. The biggest challenge, of course, is troubleshooting. No two cases are the same, and every now and again there's a head-scratcher where it's difficult to pin down the cause. Sometimes it can be something unexpected. For instance the check engine light might stay on even after you repair a short circuit, and its only after careful inspection that you discover a fuse came loose. The feeling of accomplishment when an engine starts up without issue after heavy servicing is huge, and I can't help making a little victory pose inside my head each and every time.
Truly listening to customers
Honestly I'm not very good at interacting with customers. I would much rather focus on machines, which is why I'm grateful that BMW Group technicians don't have to handle customer service. Interviewing customers about their car issues and explaining repairs is handled by the service advisers who work in the front of house, which frees up we technicians to spend that waiting time focused entirely on servicing vehicles.
That's not the same thing, however, as saying "technicians don't need to listen to customers." We only spend a few hours with our customers' cars. The customers ride them every day and are in the best position to notice when something is wrong. For instance, if a customer mentions that their car is making a noise, even if we don't notice anything abnormal during inspection something must have caught their attention. Does the noise happen when the engine is warm? When it is cool? Is it related to weather? Through our service advisers we try to get the customer's perspective and then do all we can to respond appropriately. Customers are entrusting us with a valuable part of their lives, and it's on us to return it in perfect condition.
The certification system creates a sense of accomplishment
The great thing about the Meister system is that it lets you take pride in your work. Work is interesting and rewarding, and you can always aim higher. The highest certification is BMW/MINI Meister, and when a new Meister is certified that dealer is listed on BMW Group's extranet. It's a valuable certification, and a company's status changes significantly depending on whether or not they have any Meisters working for them. Everyone knows how difficult the exam is.
There's one technician above me at the company I work for with MINI Meister certification, and he's always ready with sound advice no matter what you ask. I never stop being surprised by how much he knows! The dealerships also strive to offer opportunities to motivate technicians, such as pay increases and incentive trips for certification. That's another benefit which I think is unique to the BMW Group.
I feel very blessed to work in an environment where I can enjoy myself while also improving my skills. My goal in the immediate future is to become a senior engineer. After that I aim to reach MINI Meister one day, so that I can keep striving to provide customers with their best car life.
OTHERS
Other interviews